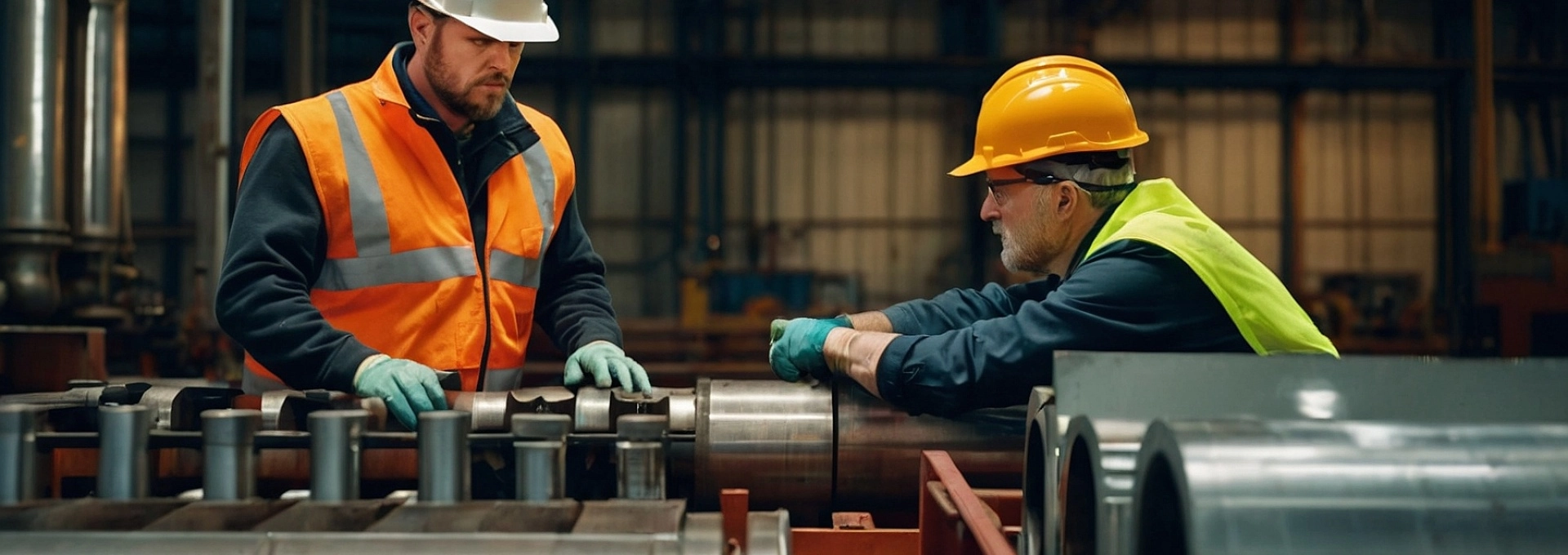
La maintenance en condition opérationnelle (MCO) constitue un enjeu majeur pour les entreprises et organisations possédant des équipements ou systèmes complexes. Cette démarche vise à garantir la disponibilité et la fiabilité des matériels sur le long terme, tout en optimisant les coûts associés. Le MCO englobe l'ensemble des activités de maintenance préventive, corrective et conditionnelle, ainsi que la gestion des ressources nécessaires. Son objectif est de minimiser les risques de panne, prolonger la durée de vie des équipements et assurer la continuité des opérations. La mise en place d'une stratégie de MCO efficace repose sur plusieurs principes clés, qui seront détaillés dans cet article.
Planification efficace des opérations de maintenance préventive
La planification des opérations de maintenance préventive constitue le socle d'une stratégie de MCO performante. Elle permet d'anticiper les défaillances potentielles et d'intervenir de manière proactive sur les équipements avant l'apparition de pannes. Cette approche préventive vise à réduire les temps d'arrêt non planifiés et à optimiser la disponibilité opérationnelle des systèmes. La mise en place d'un plan de maintenance préventif nécessite une analyse approfondie des caractéristiques techniques des équipements, de leur historique de fonctionnement et des recommandations des fabricants.
L'élaboration d'un calendrier d'interventions précis constitue une étape cruciale de la planification. Ce planning doit tenir compte des contraintes opérationnelles de l'entreprise, des cycles de production et des périodes de moindre activité pour minimiser l'impact sur les opérations. Les opérations de maintenance préventive peuvent inclure des inspections visuelles, des contrôles de paramètres, des remplacements de pièces d'usure, des calibrages ou encore des mises à jour logicielles. La fréquence de ces interventions doit être déterminée en fonction de l'analyse des données de fiabilité et de l'expérience acquise sur les équipements.
L'utilisation d'outils informatiques de Gestion de Maintenance Assistée par Ordinateur (GMAO) facilite grandement la planification et le suivi des opérations de maintenance préventive. Ces systèmes permettent de centraliser les informations techniques, de générer automatiquement des ordres de travail et de suivre l'avancement des interventions en temps réel. Ils offrent également des fonctionnalités d'analyse statistique pour évaluer l'efficacité du plan de maintenance et l'ajuster si nécessaire.
La mise en œuvre d'une maintenance préventive efficace nécessite une coordination étroite entre les différents services de l'entreprise. Les équipes de production doivent être impliquées dans la planification pour identifier les créneaux d'intervention les plus opportuns. Les techniciens de maintenance doivent disposer des compétences et des ressources nécessaires pour mener à bien les opérations prévues. Une communication fluide entre les différents acteurs est indispensable pour garantir le bon déroulement des interventions et minimiser les perturbations sur l'activité.
L'évaluation régulière de l'efficacité du plan de maintenance préventive est essentielle pour l'améliorer en continu. Des indicateurs de performance tels que le taux de disponibilité des équipements, le nombre de pannes évitées ou encore le coût de la maintenance par rapport à la valeur des actifs permettent de mesurer l'impact des actions préventives. L'analyse de ces données permet d'ajuster la fréquence et la nature des interventions pour optimiser le rapport coût/efficacité de la maintenance préventive. Pour en savoir plus sur les solutions de MCO, cliquez ici.
Gestion optimisée des pièces détachées et consommables
La gestion efficace des pièces détachées et des consommables représente un aspect fondamental du maintien en condition opérationnelle. Elle vise à garantir la disponibilité des composants nécessaires aux interventions de maintenance tout en minimisant les coûts de stockage et les risques d'obsolescence. Cette gestion implique une analyse fine des besoins opérationnels, une politique d'approvisionnement adaptée et un suivi rigoureux des flux de pièces. L'optimisation de ce processus contribue directement à la réactivité des équipes de maintenance et à la réduction des temps d'arrêt des équipements.
Stocks adaptés aux besoins opérationnels
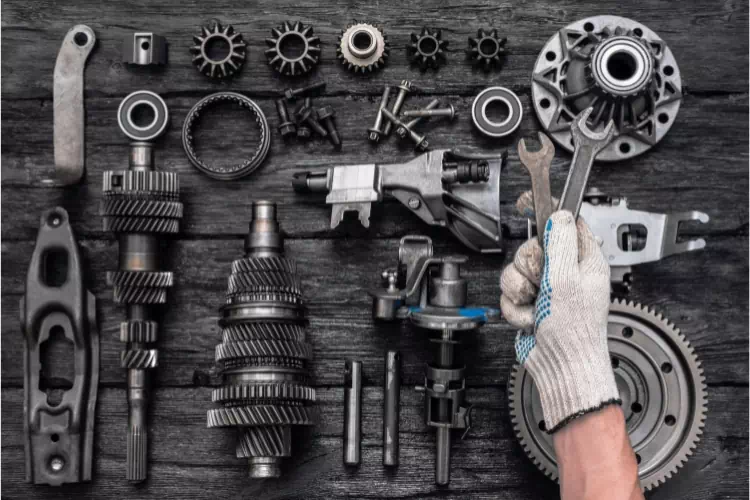
La définition des niveaux de stocks optimaux pour chaque référence de pièce détachée ou consommable constitue un défi majeur. Cette optimisation repose sur une analyse approfondie de la criticité des équipements, de la fréquence d'utilisation des pièces et des délais d'approvisionnement. L'objectif est de maintenir un stock suffisant pour répondre aux besoins courants et aux interventions planifiées, tout en évitant le sur-stockage qui immobilise inutilement des capitaux. Des méthodes d'analyse statistique, telles que la classification ABC ou l'étude des taux de rotation, permettent d'affiner la gestion des stocks en priorisant les références les plus critiques.
La mise en place d'un système de gestion informatisé des stocks facilite le suivi en temps réel des niveaux d'inventaire et la génération automatique de commandes de réapprovisionnement. Ces outils permettent également d'analyser les tendances de consommation et d'ajuster dynamiquement les seuils de commande en fonction de l'évolution des besoins. L'intégration de ces systèmes avec la GMAO offre une visibilité accrue sur les besoins futurs en pièces détachées, en lien avec le planning de maintenance préventive.
Approvisionnement stratégique auprès des fournisseurs
La mise en place d'une politique d'approvisionnement efficace implique le développement de partenariats stratégiques avec les fournisseurs de pièces détachées et de consommables. Ces relations privilégiées permettent d'obtenir des conditions tarifaires avantageuses, des délais de livraison réduits et une meilleure réactivité en cas de besoins urgents. La négociation de contrats-cadres avec les principaux fournisseurs offre une visibilité à long terme sur les approvisionnements et peut inclure des clauses de stock de sécurité chez le fournisseur pour les pièces critiques.
L'évaluation régulière des performances des fournisseurs, basée sur des critères tels que la qualité des pièces livrées, le respect des délais ou encore la réactivité en cas d'urgence, permet d'optimiser en continu la chaîne d'approvisionnement. La diversification des sources d'approvisionnement pour les pièces critiques contribue à réduire les risques de rupture de stock en cas de défaillance d'un fournisseur. L'exploration de solutions alternatives, telles que la fabrication additive pour certaines pièces spécifiques, peut également offrir des opportunités d'optimisation des coûts et des délais d'approvisionnement.
Traçabilité rigoureuse des pièces utilisées
La mise en place d'un système de traçabilité performant pour les pièces détachées et les consommables constitue un élément clé de la gestion des stocks dans le cadre du MCO. Cette traçabilité permet de suivre précisément l'utilisation des pièces, depuis leur réception jusqu'à leur installation sur les équipements. L'enregistrement systématique des mouvements de stock, associé à l'identification unique de chaque pièce critique, offre une visibilité totale sur l'historique des interventions et facilite les analyses de fiabilité.
L'utilisation de technologies telles que les codes-barres ou les puces RFID simplifie la gestion des flux de pièces et réduit les risques d'erreur. Ces systèmes permettent une mise à jour en temps réel des niveaux de stock et une allocation précise des coûts de maintenance par équipement. La traçabilité des pièces contribue également à la gestion de la qualité en facilitant l'identification et le rappel éventuel de lots défectueux. Elle joue un rôle essentiel dans le respect des exigences réglementaires, particulièrement dans les secteurs soumis à des normes strictes comme l'aéronautique ou le nucléaire.
Indicateur | Valeur cible | Impact sur le MCO |
---|---|---|
Taux de rotation des stocks | 4 à 6 rotations/an | Optimisation des coûts de stockage |
Taux de service (disponibilité des pièces) | 95% minimum | Réduction des temps d'arrêt |
Délai moyen d'approvisionnement | < 5 jours ouvrés | Amélioration de la réactivité |
Formation continue des équipes techniques spécialisées
La formation continue des équipes techniques constitue un pilier fondamental du maintien en condition opérationnelle. Elle vise à garantir que les personnels chargés de la maintenance disposent en permanence des compétences nécessaires pour intervenir efficacement sur des systèmes de plus en plus complexes et en constante évolution. Cette démarche de formation s'inscrit dans une logique d'amélioration continue des performances et d'adaptation aux innovations technologiques. Elle contribue directement à la qualité des interventions, à la réduction des temps d'arrêt et à l'optimisation des coûts de maintenance.
Programmes adaptés aux évolutions technologiques
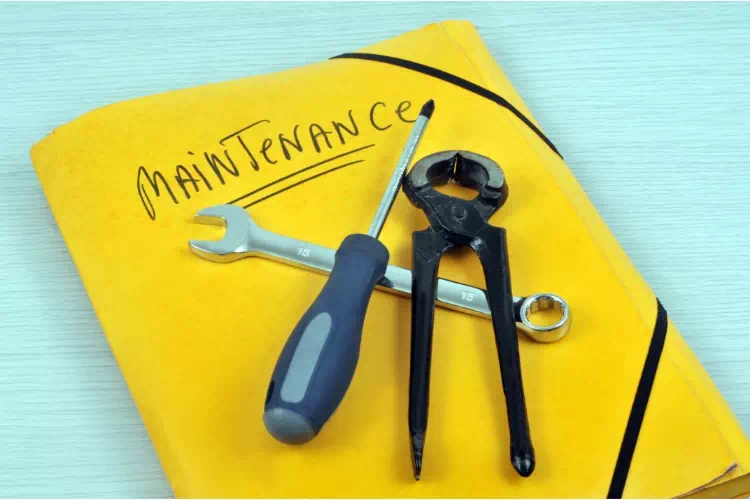
L'élaboration de programmes de formation adaptés aux évolutions technologiques constitue un défi majeur pour les organisations. Ces programmes doivent couvrir un large spectre de compétences, allant des connaissances techniques spécifiques aux équipements jusqu'aux méthodologies de diagnostic et de résolution de problèmes. L'intégration de modules sur les nouvelles technologies, telles que l'Internet des Objets (IoT) ou l'intelligence artificielle appliquée à la maintenance prédictive, permet d'anticiper les besoins futurs en compétences. La collaboration avec les fabricants d'équipements et les centres de formation spécialisés est essentielle pour élaborer des contenus pédagogiques pertinents et à jour.
L'utilisation de méthodes pédagogiques innovantes, comme la réalité virtuelle ou augmentée, offre de nouvelles perspectives pour la formation technique. Ces technologies permettent de simuler des interventions complexes ou dangereuses dans un environnement sécurisé, favorisant l'acquisition de compétences pratiques sans risque pour les équipements. La mise en place de parcours de formation personnalisés, tenant compte des compétences initiales et des objectifs de progression de chaque technicien, optimise l'efficacité des programmes de formation et la motivation des équipes.
Mise en situation réaliste régulière
La mise en situation régulière des équipes techniques dans des conditions proches de la réalité opérationnelle constitue un élément clé de la formation continue. Ces exercices pratiques permettent aux techniciens de confronter leurs connaissances théoriques à des cas concrets, renforçant ainsi leur capacité à réagir efficacement face à des situations imprévues. L'organisation de sessions de travail sur des équipements réels ou sur des simulateurs haute-fidélité favorise le développement des compétences techniques et des réflexes opérationnels.
La mise en place de scénarios de pannes complexes, reproduisant des situations critiques rencontrées sur le terrain, permet d'évaluer la capacité des équipes à diagnostiquer rapidement les problèmes et à mettre en œuvre les solutions appropriées. Ces exercices contribuent également à renforcer la cohésion des équipes et à améliorer la communication entre les différents intervenants. L'analyse des performances lors de ces mises en situation permet d'identifier les axes d'amélioration et d'ajuster en conséquence les programmes de formation.
Évaluation périodique des compétences acquises
L'évaluation régulière des compétences techniques acquises par les équipes de maintenance constitue un élément essentiel pour garantir l'efficacité du programme de formation continue. Cette démarche permet de mesurer l'évolution des connaissances et savoir-faire des techniciens, d'identifier les éventuelles lacunes et d'ajuster les plans de formation en conséquence. La mise en place d'un système d'évaluation structuré contribue à maintenir un niveau élevé de qualification des équipes, en adéquation avec les exigences opérationnelles et les évolutions technologiques.
L'utilisation de méthodes d'évaluation variées permet d'obtenir une vision complète des compétences des techniciens. Les tests théoriques permettent de vérifier l'acquisition des connaissances fondamentales, tandis que les épreuves pratiques sur des équipements réels ou simulés évaluent la capacité à mettre en œuvre ces connaissances dans des situations concrètes. L'observation des interventions sur le terrain par des experts permet d'apprécier les compétences comportementales, telles que la rigueur méthodologique, la capacité d'analyse ou encore l'aptitude au travail en équipe.
La fréquence des évaluations doit être adaptée au rythme d'évolution des technologies et des procédures de maintenance. Une périodicité annuelle constitue généralement un bon compromis, permettant de suivre la progression des techniciens tout en limitant la charge administrative liée au processus d'évaluation. Pour les domaines particulièrement critiques ou en rapide évolution, des évaluations plus fréquentes peuvent être nécessaires.
L'analyse des résultats des évaluations permet d'établir des plans de développement individualisés pour chaque technicien. Ces plans identifient les axes de progression prioritaires et définissent les actions de formation complémentaires à mettre en œuvre. L'implication des techniciens dans ce processus, à travers des entretiens d'évaluation et de feedback, favorise leur engagement dans une démarche d'amélioration continue de leurs compétences.
Suivi rigoureux des indicateurs de performance clés
Le suivi des indicateurs de performance clés (KPI) constitue un élément fondamental dans la gestion efficace de la maintenance en condition opérationnelle. Cette approche permet de mesurer objectivement l'efficacité des processus de maintenance, d'identifier les axes d'amélioration et de prendre des décisions basées sur des données concrètes. La mise en place d'un tableau de bord complet et pertinent offre une visibilité en temps réel sur l'état des équipements et l'efficacité des interventions, facilitant ainsi le pilotage opérationnel et stratégique de la maintenance.
La sélection des indicateurs de performance doit être réalisée avec soin pour refléter les objectifs spécifiques de l'organisation en matière de maintenance. Parmi les KPI couramment utilisés, on peut citer le taux de disponibilité des équipements, le temps moyen entre pannes (MTBF), le temps moyen de réparation (MTTR), le taux de réalisation du plan de maintenance préventive ou encore le coût de maintenance par unité de production. Ces indicateurs doivent être complétés par des mesures de la qualité des interventions, telles que le taux de réussite des réparations au premier essai ou le nombre de réclamations clients liées à des problèmes de maintenance.
L'utilisation d'outils informatiques de Business Intelligence facilite la collecte, le traitement et la visualisation des données de performance. Ces systèmes permettent de générer automatiquement des tableaux de bord dynamiques, offrant une vue d'ensemble de la performance de maintenance ainsi que la possibilité d'analyser en détail chaque indicateur. La mise en place d'alertes automatiques en cas de dépassement de seuils critiques permet une réaction rapide face aux dérives potentielles.
Indicateur | Objectif | Fréquence de suivi |
---|---|---|
Taux de disponibilité des équipements | 98% | Quotidienne |
Temps moyen entre pannes (MTBF) | 500 heures | Mensuelle |
Taux de réalisation du plan de maintenance préventive | 95% | Hebdomadaire |
Coût de maintenance par unité produite | Réduction de 5% annuelle | Trimestrielle |
L'analyse régulière des indicateurs de performance, tels décrits dans le tableau précédent permet d'identifier les tendances à long terme et d'évaluer l'impact des actions d'amélioration mises en œuvre. Cette analyse doit être réalisée de manière collaborative, impliquant les équipes de maintenance, de production et de gestion. Des réunions périodiques de revue de performance permettent de partager les résultats, d'identifier les causes profondes des écarts par rapport aux objectifs et de définir les plans d'action correctifs.
La comparaison des performances avec des références externes, à travers des exercices de benchmarking, offre une perspective supplémentaire sur l'efficacité des processus de maintenance. Cette démarche permet d'identifier les meilleures pratiques du secteur et de fixer des objectifs ambitieux mais réalistes. La participation à des groupes de travail inter-entreprises ou à des associations professionnelles facilite l'échange d'expériences et la diffusion des innovations en matière de gestion de la maintenance.
Amélioration continue des processus de maintenance opérationnelle
L'amélioration continue des processus de maintenance opérationnelle constitue un axe stratégique majeur pour optimiser la performance globale du maintien en condition opérationnelle. Cette démarche systématique vise à identifier et mettre en œuvre des actions d'amélioration à tous les niveaux de l'organisation de maintenance, depuis les interventions techniques jusqu'aux processus de gestion et de planification. L'objectif est de réduire les coûts, d'accroître l'efficacité des interventions et d'augmenter la fiabilité des équipements sur le long terme.
La mise en place d'une culture de l'amélioration continue au sein des équipes de maintenance nécessite l'implication de tous les acteurs, du technicien de terrain jusqu'à la direction. L'encouragement des initiatives individuelles et collectives, à travers des programmes de suggestions ou des groupes de résolution de problèmes, permet de capitaliser sur l'expertise et la créativité des équipes opérationnelles. La formation des personnels aux méthodologies d'amélioration continue, telles que le Lean Maintenance ou le Six Sigma, fournit les outils nécessaires pour analyser les processus et identifier les opportunités d'optimisation.
L'analyse systématique des données de maintenance constitue un levier puissant pour l'amélioration continue. L'exploitation des informations collectées à travers les systèmes de GMAO et les capteurs IoT permet d'identifier les équipements les plus problématiques, les modes de défaillance récurrents ou encore les inefficacités dans les processus d'intervention. L'utilisation de techniques d'analyse avancées, comme le data mining ou le machine learning, offre de nouvelles perspectives pour détecter des patterns cachés et anticiper les besoins de maintenance. En résumé, la maintenance opérationnelle assure :
- Analyse des causes racines (RCA) pour chaque panne majeure
- Mise en place de cercles de qualité inter-services
- Révision périodique des procédures de maintenance
- Benchmarking des pratiques de maintenance avec d'autres industries
- Intégration des retours d'expérience dans les plans de formation
La révision régulière des stratégies de maintenance pour chaque équipement critique permet d'optimiser l'équilibre entre maintenance préventive, prédictive et corrective. Cette approche, basée sur l'analyse des données de fiabilité et de coûts, vise à maximiser la disponibilité des équipements tout en minimisant les coûts globaux de maintenance. L'introduction progressive de technologies de maintenance prédictive, telles que l'analyse vibratoire ou la thermographie infrarouge, permet d'anticiper les défaillances et d'intervenir au moment optimal, réduisant ainsi les temps d'arrêt non planifiés.
L'amélioration des processus logistiques liés à la maintenance, notamment la gestion des pièces détachées et des outillages, contribue significativement à l'efficacité globale des interventions. L'optimisation des flux de pièces, la rationalisation des stocks et la mise en place de partenariats stratégiques avec les fournisseurs permettent de réduire les délais d'intervention et les coûts de possession. L'utilisation de technologies comme la fabrication additive pour la production de pièces de rechange à la demande ouvre de nouvelles perspectives pour la gestion des pièces obsolètes ou à faible rotation.